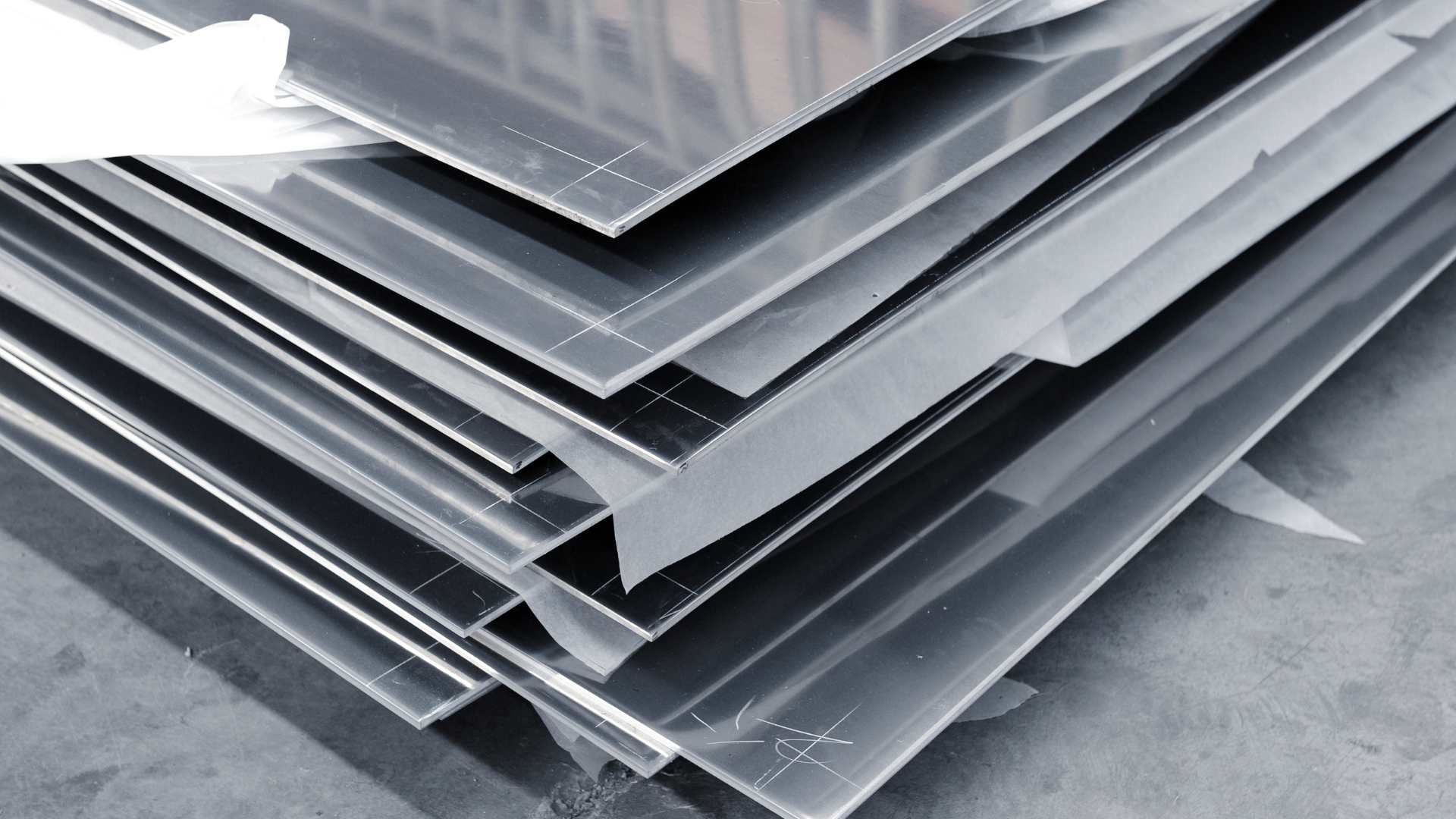
Aluminium Treatment
Aluminium is notorious in industrial metal finishing for it’s alloys
On this page, we look at the treatment of Aluminium. Aluminium is notorious in industrial metal finishing for it’s alloys and the quality of any alloy will inevitably affect the finished product. Alloys with high silicon content can cause all sorts of problems, even for the most experienced plater; so don’t worry if you have issues -you’re in good company!
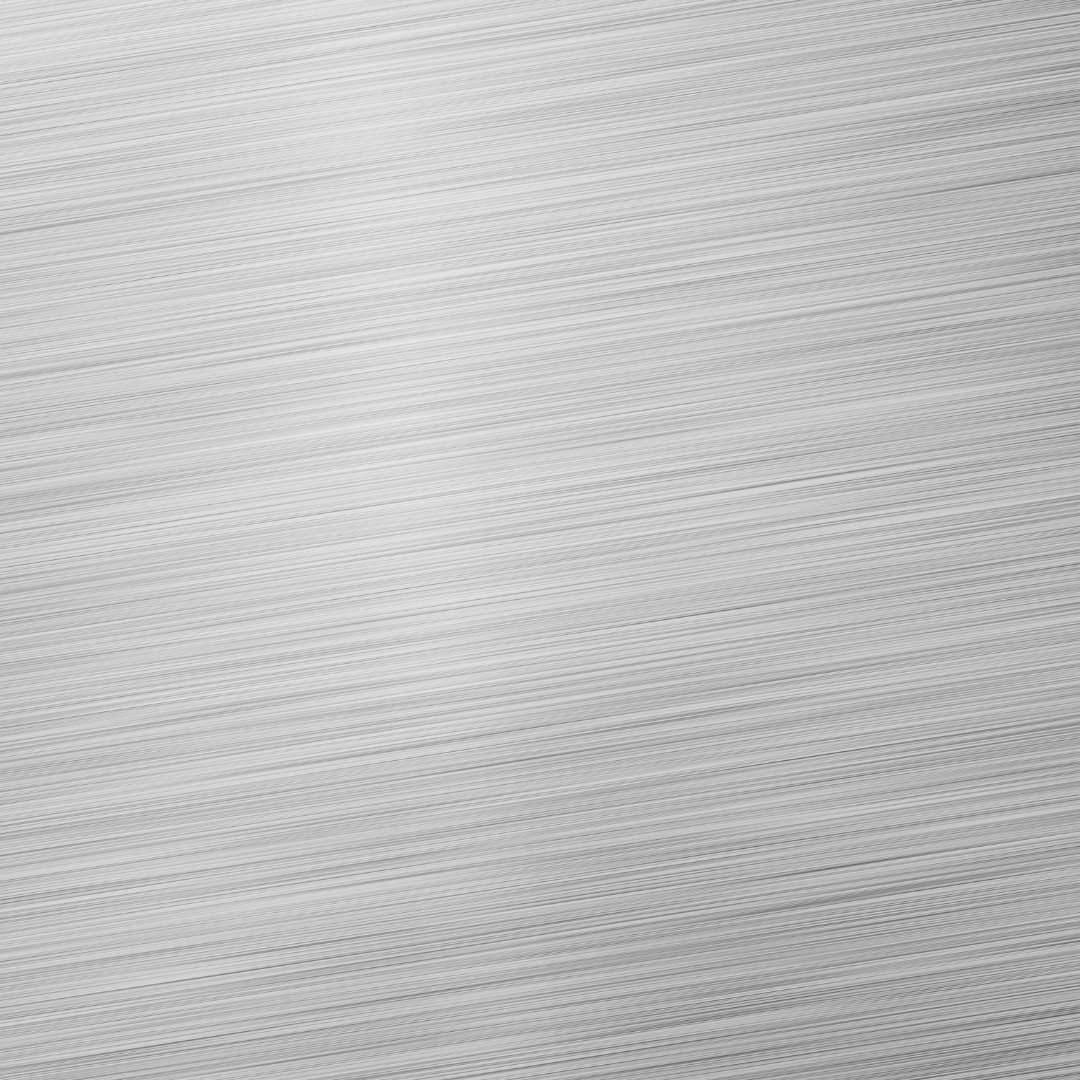
Aluminium
Etching
The etching of Aluminium is a very common process and reasonably simple to perform. Often aluminium process needs to be performed very carefully and can often be etched accidentally by inappropriate chemistry. However, controlled etching is an important process in aluminium treatment and our etch products are used in industrial practices every single day.
The Youplate Aluminium Etch is not just a base material, but a formulated product which allows for the controlled etching of components which being formulated using chelating agents to allow for a long bath life and avoid inevitable metal composition in the solution which will ruin a solution. The nature of the formula allows for dissolved aluminium to create a “complex” which does not produce hard deposits within the tank and will allow for a long bath life and therefore saving costs. The etch solution can also be used to remove anodising and “alochrome” coatings on the surface of components.
Aluminium etching products
-
Aluminium ACUbond Zincate Solution
Regular price £19.00 GBPRegular priceUnit price / per -
18G High Grade Aluminium Wire
Regular price £6.99 GBPRegular priceUnit price / per -
High Grade Lead Anodes / Cathodes
Regular price £9.00 GBPRegular priceUnit price / per -
Aluminium Acuseal 30 - Low temperature anodising sealer
Regular price £9.49 GBPRegular priceUnit price / per -
Aluminium De-Smut, HyperBrite Deox AL
Regular price From £9.99 GBPRegular priceUnit price / per -
Acidic Cleaner, 1 Litre
Regular price £12.99 GBPRegular priceUnit price / per
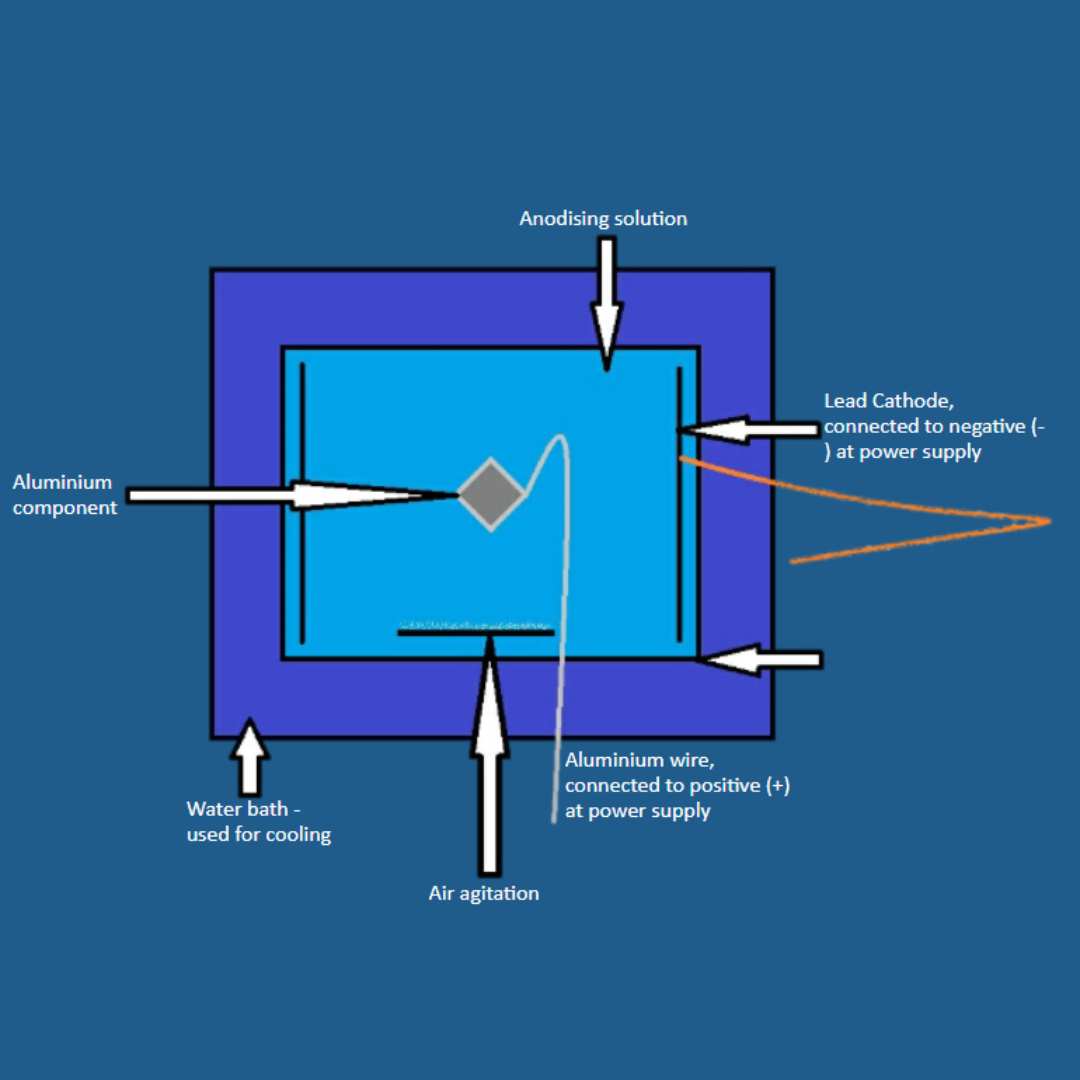
Aluminium
Anodising
This is a diagram detailing a basic home set-up for an anodising process. The process is electrolytic and unlike standard electroplating, the treated articles must be connected to the positive connection at the power source. The treated articles are the ANODE. The Cathode (negative) this must be made from high quality lead.
The anodising process imparts a protective film on the surface of the treated aluminium. This treatment also allows the addition of colour to enable treated parts to be afforded an attractive yet resistant coating.
This section of our site will give a little insight into the process. Our products are formulated with ease of use and value in mind so that getting an industrial quality finish is within reach to a range of budgets.The anodising process imparts a protective film on the surface of the treated aluminium. This treatment also allows the addition of colour to enable treated parts to be afforded an attractive yet resistant coating.
This section of our site will give a little insight into the process. Our products are formulated with ease of use and value in mind so that getting an industrial quality finish is within reach to a range of budgets.
Anodising process
-
Cooling
Cooling an anodising solution is one of the first things any user must consider when examining the use of this process. In simple terms, the process gets hot -the hotter it gets, the worse it performs. Therefore any way a user can keep a solution from getting hot will be appreciated in the results attained. Industrial anodisers use refrigerants and expensive cooling systems. In small applications, uses might consider using an outer containment tank which can house cold water and / or ice to keep the solution temperature from rising too much.
-
Agitation
Agitating your solution is essential for an evenly distributed, quality finish. Whilst it is entirely possible to attain a reasonable finish without any solution agitation, it is recommended that the use of air to agitate the anodising solution be employed. Using small fish tank pumps mean that it’s not an expensive addition -just make sure that anything you put in the tank is not liable to damage by the acidic solution.
-
Sealing
Newly anodised work, whether it has been dyed or not, MUST be sealed. Sealing is traditionally performed by immersing in boiling water for the same time in which anodising took place, for example; anodise for 1 hour - seal for 1 hour. The water must be kept hot throughout this process and not allowed to cool as imperfect and ineffective sealing will be observed. This process can be reduced greatly by adding a sealing additive.
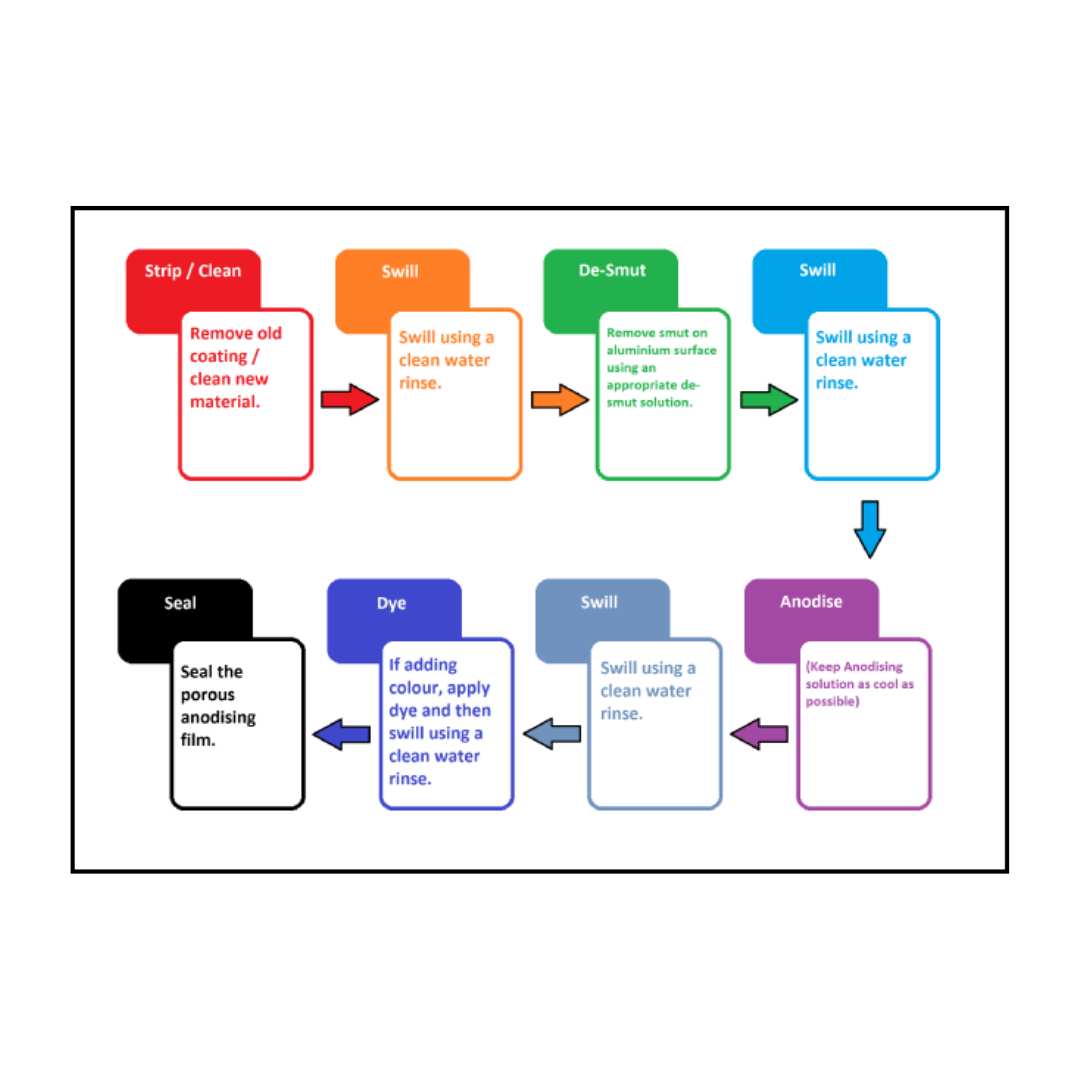
Current Density 10 – 15 amps / ft²
Voltage Up to 16 Volts for normal anodising
Temperature Up to 30°C (cool to below this temperature)
Agitation Vigorous air agitation is recommended to attain consistent results. Ensure the material used is resistant to acid.
Time 30 minutes – 1 hour (Anodising film thickness will often stop increasing after 90 minutes.)
Zincate
ACUbond zincate solution is a non-cyanide zincate process designed specifically to facilitate plating of metallic deposits on aluminium alloys. ACUbond applies a thin dense zincate film that can be subsequently plated with copper, nickel, electro-less nickel and other metals.
This process is a formulated product that is EXACTLY the same as supplied to industrial users and is manufactured with the same high standards of quality as any of our other formulated processes.
A liquid product using more complex chemistry to alternatives available online and gives excellent results and improved adhesion between aluminium and subsequent electroplated deposit.

Contact us
Whilst there is a lot of information available online, we will try not to overload users of this web site with information which may not always be needed, so if there is a question you may have regarding you electroplating, please feel free to contact us.